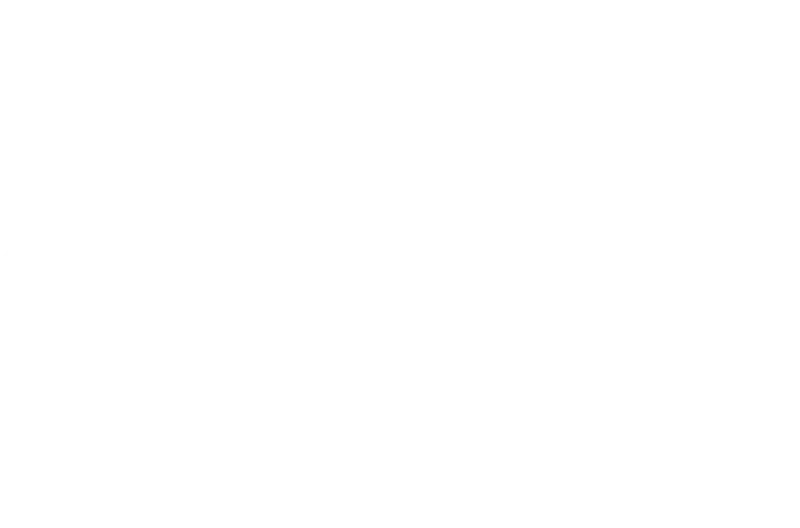
For more than 50 years, Colonial Saw has shared a proud partnership with STRIEBIG based on shared values of uncompromising quality, timeless craftsmanship, and dedicated service to our customers.
These philosophies have guided us toward building a lasting connection and unshakable commitment to sales, service, and technical expertise that is reflected in everything we do. Our steadfast collaboration is well-engineered to deliver on a simple promise: provide peak performance that stands unequaled among the rest.
When you think vertical panel saws, think STRIEBIG. Think Colonial Saw.

Setting the Standard in Vertical Panel Saws
Efficiency, simplicity, accuracy, precision—one name integrates all these qualities in its vertical panel saws—STRIEBIG.
Only STRIEBIG provides the legendary quality against which other panel saws are measured.
Manufactured in Switzerland by the world's finest engineers, STRIEBIG is dedicated to producing the finest vertical panel saw systems available today. Through meticulous quality, ease of operation, and steadfast dependability, STRIEBIG solutions open new worlds of cutting capabilities to fit any commercial need with maximum precision and minimal floor space.
Colonial Saw is your connection. As North America's exclusive importer of STRIEBIG vertical panel saws, we stand behind their impressive history of safety and performance and provide the cutting versatility to match your unique application – all contained within one space-saving and precise machine.
What makes STRIEBIG the international benchmark in vertical panel saws?
Why do customers choose Colonial Saw?
Unrivaled Knowledge & Experience
Decades of strict focus on vertical panel saws for woodworking machinery.
Proven Support Infrastructure
Nationwide network, easy parts ordering, mobile service & support.
Access to Colonial Saw's Network
Factory-trained technicians for the East Coast, West Coast & Mid-West.
Our Passionate and Dedicated Staff
Over 50 years of expert sales, service, and technical expertise as an official U.S. importer.
Manual Panel Saws
Manual saws are ideal for commercial operations such as custom cabinet makers and woodworking businesses of all sizes.
Flexible Entry Level Saw
Cut Capacity 10'2" W x 5'5" H
Cut Depth 2-3/8"
Saw Motor 5-1/4hp
Main Blade 250mm
Back Support
Wood Small Parts Area
Scoring Saw Optional
Measurement System Analog (Tape Measure) (Digital Available)
Larger Sizes & More Features
Standard Cut Capacity 15'1" W x 5'5" H (Larger Sizes Available)
Cut Depth 2-3/8"
Saw Motor 5-1/4hp
Main Blade 250mm
Back Support
Wood Small Parts Area
Scoring Saw Optional
Measurement System
X-Axis (Vert. Cuts) - Analog
Y-Axis (Horz. Cuts) - Digital
(X Axis Digital Available)
Proven Universal Saw
Standard Cut Capacity 14'1" W x 5'6" H (Larger Sizes Available)
Cut Depth 3-1/8"
Saw Motor 7-1/2 hp
Main Blade 300mm
Back Support All Aluminum, All Wood, or Wood Small Parts Area
Scoring Saw NA
Measurement System Analog (Tape Measure) (Digital Available)
Flexible Universal Saw
Standard Cut Capacity 14'1" W x 5'6" H (Larger Sizes Available)
Cut Depth 3-1/8"
Saw Motor 7-1/2 hp
Main Blade 300mm
Back Support All Aluminum, All Wood, or Wood Small Parts Area
Scoring Saw Optional
Measurement System Analog (Tape Measure) (X-Axis Digital Available, Y-Axis Digital Available in Comfort Package*)
*Optional Comfort Package Auto-locking support rollers, digital measuring for the Y-axis with motorized fine adjustment, pneumatic carriage clamping, and the laser cut line guide for horizontal cuts.
Semi-Automatic Panel Saws
Semi-auto saws are ideal for panel processors and woodworking businesses looking to ehnhance effciency by balancing automation and manual control.
Versatile Panel Saw
Cut Capacity 17’4” W x 7’4” H
Cut Depth 3-1/8"
Saw Motor 7-1/2 hp
Main Blade 300mm
Control Push Button
Back Support All Wood
Scoring Saw Optional
Measurement System
Digital
Automation Features
Panel lifters (lowering units) that allow for easy one-person panel processing.
Bottom Panel Triming Available (Multiple Panels)
Comfort Package Standard Auto-locking support rollers, digital measuring for the Y-axis with motorized fine adjustment, pneumatic carriage clamping, and the laser cut line guide for horizontal cuts.
Entry Level Automatic Saw
Standard Cut Capacity 14’1” W x 5’6” H (Larger Sizes Available)
Cut Depth 3-1/8"
Saw Motor 7-1/2 hp
Main Blade 300mm
Control 12" Touch Screen
Back Support All Wood
Scoring Saw Optional
Measurement System
X-Axis Digital
Y-Axis Digital w/Auto Fine Adj.
Automation Features
Auto-locking saw beam and support rollers
Auto clamping, pivoting, and plunging of saw head
Tool Database
Bottom Panel Triming NA
Automatic Panel Saws
Automatic saws are well-suited for woodworking businesses looking to reduce labor and increase effciency.
Premium Automatic Saw
Standard Cut Capacity 14’1” W x 5’6” H (Larger Sizes Available)
Cut Depth 3-1/8"
Saw Motor 7-1/2 hp
Main Blade 300mm
Control 12" Touch Screen
Back Support All Wood
Scoring Saw Optional
Measurement System
X-Axis Digital (EPS Available)
Y-Axis EPS (Electronic Positioning)
Sawing Process Fully Automatic 0.3-82 feet/min
Bottom Panel Triming Available (Single Sheet)
Automatic High-End Saw Center
Standard Cut Capacity 17’4” W x 7’4” H (Larger Sizes Available)
Cut Depth 3-1/8"
Saw Motor 7-1/2 hp
Main Blade 300mm
Control 12" Touch Screen
Back Support All Wood
Scoring Saw Optional
Measurement System
X-Axis Digital (EPS Available)
Y-Axis EPS (Electronic Positioning)
Sawing Process Fully Automatic 0.3-82 feet/min
Bottom Panel Triming Available (Multiple Panels)
Optional CNC Integration Panel Lifters and Programable Pusher
Panel Saw Resources
Striebig FAQs
Striebigs can be as small as 70 sq. ft. (Compact) or as large (in the largest standard frame sizes) as 134 sq. ft. Besides the space that the machine occupies, you need room to load, operate, and unload the machine. That will depend on the size of the sheets you are cutting and how you are storing and bringing them to and onto the saw. Generally you will want more room to the right side of the saw for loading full sheets, and less room is required to the left where you will be off-loading finish cut pieces.
Yes, with the Striebig expert cut optimizing allows you can go screen to machine on a Control or Striebig 4D
All Striebig machines have dust hose (and pipe) to get the dust from the saw head to the back of the machine. All machines prior to 1993 had fans inside the housing to propel dust into a dust bag, so a collector was not required. From 2005 on all models require a dust collector, but are much more efficient in their dust pick-up. All Standard III, Automat III, Compacts, Evolution and Control models require collectors. Standard II models up to 2005 do not require them, but Standard TRK models from 2005 on do. Compacts have 4” diameter ports (Compacts after 2004 have a second optional 4” port on the bottom right of the frame) and require 500cfm/port for wood dust. All others models have either single 160mm or 140mm ports (depending on year) or can be connected to two 4” ports, and generally require 1000 cfm. You may contact us at Colonial Saw for more detailed specs regarding speed, pressure, etc.
Most Striebig models do not require air, however, a Compact Automatic, Evolution, Control, and a Standard TRK with the optional pneumatic locking rollers do. They do not consume much volume, but would require a supply of 100 psi min. The air controls such things as the locking rollers, and the locking of the saw beam and pivoting of the saw head on the Evolution and Control. The critical function of shifting the grid so the saw blade does not cut into it, is a mechanical system on all models and does not use air.
A Compact or current Compact Plus can fit under an 8’ ceiling. They are 7’ 10-1/2” at the highest point, except for the repeat rip device scale, which extends to 8’ 6” high when the saw head is all the way to the top. If this is an issue, then you can choose the smaller repeat rip device, which will keep it within the 7’ 10-1/2”, or physically limit the height to which you bring the saw head, if you only cut 4’ material. A Standard model (of _168 frame height) has a height of only 7’8” and an Evolution or Control (also of _168 frame height) is 8’ 1-1/2”.
The answer has two parts:
- A riving knife behind the saw blade prevents the board from pinching.
- As the saw cuts from left to right, the operator, positioned behind or to the left, can manage the top piece with the left hand or both hands if it's an automatic saw. For small pieces (up to 12”), they hold it from the top or press it against the back support as the saw exits to the right. For larger pieces, like a 4’x8’ board, they insert a wood wedge from the tool kit into the saw kerf past the halfway point to act as a fulcrum, opening the cut as the saw finishes.
Yes! Stack-cutting is a nice advantage of a vertical panel saw over a table saw or slider. Compacts can handle up to 2-3/8” of material or 3 sheets of ¾”. All other Striebigs have a 3-1/8” depth of cut or 4 sheets of ¾” material capacity! An Evolution or Control can be special-ordered to go up to 4” depth, and the new 4D model can go up to 5” depth! In the real world, we mostly see up to two sheets at a time cut on Compacts and maybe three sheets on the other models. Material handling can become more the issue than the saw’s ability to cut it. What is more common is to start with a single sheet, but then once it has been cut into more manageable pieces, then those pieces are put back on the saw 2 or 3 at a time and cut into like parts, like the two sides of a cabinet. This can add up to a lot of time savings over a table saw or slider!
Gravity! The panel rests on either the support rollers on the bottom or the center shelf fingers, if it is smaller. The saw frame is leaning back at a 5-degree angle, so the piece just sits there nicely. There is a little bit of spring tension in the shroud (guard) that covers the blade to help hold the material and dampen vibration. In terms of right to left movement, friction holds the piece in place on the center shelf. The rollers on the bottom of a Compact have a flip-up panel stop on the right side to keep the panel from rolling away as you make a horizontal rip cut. On a Standard model there are foot-pedal operated locking rollers (factory option on Compacts), and on Compact Automatics, Evolution, and Control models the rollers lock automatically (pneumatically) during a cut (optional upgrade on Standard TRKs).
Yes! Since Ludwig Striebig invented his machine in the late ‘50s, Striebig has always been focused on the finish cut and cut quality. Some materials, including melamines, developed in the last 30 years have more sensitive coatings and therefore require scoring on one side in order to have a good clean cut on both sides of the sheet. There are two methods of scoring employed on most Striebig models. Over 20 years ago, Striebig developed its first true scoring saw unit, and has continued to develop and improve this concept to this day. They are belt-driven units that use split-blade type scoring saw blades. The two blades are adjusted for width either with shims in its simplest version, or by the simple turn of the T-handle Allen wrench in the advanced adjustable (“Quick-set”) version. This blade is even available in diamond for extra-long life. These scoring saw units are available on all Striebig models except the Standard TRK. Striebig has never entertained the idea of scoring panels with an inexpensive, “scratch-knife” type of scoring that others employ. These systems simple do not work very well on a wide variety of materials, and you never see them used on other types of saws, like sliding table saws or beam saws, so…
The other method of scoring widely used on Striebig saws without the optional scoring saw, is the back-scoring or climb-cut scoring method, where the main blade is used to score the panel. On a vertical panel saw, the side of the panel that is up against the backing grid is the side that will get the reliably good finish cut (like the top side when you’re using a table saw). It’s the side you’re looking at that is the side that needs scoring. When you use the back-scoring method for a vertical cut, you start with the saw head at the bottom. You plunge in until the saw blade just touches the panel (the riving knife can serve very nicely as a depth stop in this position- the blade is just a bit deeper than the riving knife), and you bring the saw head up to the top of the panel. You see the score mark right in front of you. At the top of the panel you plunge the saw to full depth and make your normal separating cut to the bottom. But then just leave the saw at the bottom, so you can start your next cut. You’ve completed one cut cycle. You’ve just started and ended the cycle in a different place. It’s the same amount of work! And the same blade that did the scoring did the cutting, so there are no alignment issues- simple! The same concept applies to horizontal cuts. When you have to score enough panels, or are using an automatic saw, a scoring saw unit will pay for itself in reduced saw sharpening bills.
The tallest panel will depend on your frame size. A Compact, manual or automatic, can fit a 65” tall panel. Taller Compacts can handle up to 81.5” or 86.5” tall panels. All other models can handle similar height panels for the standard height machines, but can also be special-ordered to handle panels up to 9’ or 10’ tall!! In terms of length, without having to roll a panel through the saw, (which is a possibility on a Striebig, because of the heavy-duty, precision rollers), you can cut up to 10’2”, 15’1”, or 17’6” on Compact models. On all other Striebigs, you can cut 10’10”, 14’1” or 17’4” on standard frames, but they can be special-ordered to cut 20’8”, 24’, 30’6” or even up to 50’!!!
That is a tricky question that we get regularly and needs further definition. If you are asking what the smallest piece you can start with and cut down further, the official traditional answer is 8” x 20”. But these days with the built-in wood small parts support area on Compacts (optional on Standard TRKs) and full wood support area on Evolution and Control, the origin piece can be far shorter in height than 8”, probably as little as 1” tall. Also, all of the machines now have center shelf fingers that can be repositioned along the center shelf bar. You should have at least two fingers supporting at least one side of a vertical cut, so approximately 4-6”. The shroud will only allow you to get so close to the support surface for a horizontal rip cut. On a Compact or Standard, that is about 1-1/4”. On an Evolution or Control, that is about 2-3/8”.
With proper care and maintenance, a Striebig vertical panels saw can last for decades.
All Striebig machines are 3-phase, but many shops run them perfectly with a rotary-type phase converter, which converts 220V single-phase power to 240V 3-phase power. There are several manufacturers of quality phase converters, but make sure you select a reputable one. They can usually run up to three machines, as long as you start the largest horsepower machine first. You will need to size the phase converter at a minimum of 1-1/2 to 2 times the horsepower of the machine, so a Compact or an old Econom would require a 7.5hp minimum converter, but 10hp is recommended. All other Striebigs should run on 15hp converters.
In almost all cases, no. Unless you are already intimately familiar with the use of vertical panel saws and have moved, re-installed, squared, and calibrated your previous Striebig more than once, we strongly do not recommend trying to install a new Striebig yourself. It should be done by a certified Striebig dealer technician or Colonial Saw. Besides the proper assembly, squaring confirmation, and calibration, a certified installation technician will train you on the proper use of the machine and its accessories, and maintenance of your machine. That alone can be worth many hours of reading the operating manual and then trying to relay that information to others, not to mention the possible wear or damage to your machine without this information.
You can order parts from your local Striebig dealer. If you do not have a relationship with your local Striebig dealer, you may contact Colonial Saw and order parts with a credit card, if you do not already have an account. We stock most parts for all Striebig models going back 30+ years. It is important to have your Striebig saw information, such as model, “type” (which is actually the frame size), serial # (usually 5 digits starting with 1-4), and year of construction (mo.yr). This information should be on a nameplate that is on the carriage (the part that goes up and down the beam and holds the saw head). Only on very old saws is this nameplate on the motor itself.
Every new Striebig machine is warranted against defective parts, including electrical components, for a period of one year from the date of service, including parts and labor. But you need to contact your local Striebig dealer or Colonial Saw for approval to insure that the part in question is covered under warranty before returning it or ordering a replacement part.
Most options are retrofittable- Except grooving/dadoing but varies by saw model.
A manual Striebig saw, like a Compact, is going to be about 3-4 times as efficient as cutting sheets on a table saw, so add up the time you take cutting it that way and divide by 3 or 4. If you spend 10 hrs./week to cut parts on a table saw, on a Striebig it will take about 3 hrs. That saves 7 hrs./week. If the cost of those hours is $18/hr., all in, then that is $126 savings/week, or (x 4.3 weeks/month) $546, which is about the lease payment on a Compact including delivery and installation (depending on location). Not only do you gain efficiency to cover the cost, you are working safer, saving space, getting much better cut quality and square parts, which reduce downstream processing time.
Saw blades are designed specifically for different materials and applications. You do not want to use the same blade to cut particle board core melamine that you use for solid surface. You do not have to buy blades from us, but we do stick blades for various applications. The blade that comes included with every Striebig saw from the start is a hollow-face blade that is very good for cutting melamine and veneer plys with a nice clean, crisp edge. It has a concave face to the tooth which produces a sharp point on the upper corners of the teeth. Not every sharpener has the equipment to sharpen this blade properly. We have a partial list of those sharpeners on the website. But we also have available a premium HATB (high alternate top bevel) blade to cut more delicate melamines and veneers. If you cut solid surface or aluminum, there are blades specific to those materials that have more teeth in a TCG (triple chip grind) configuration with a negative rake/hook angle (teeth are leaning back). Many people prefer an ATB (alternate top bevel) blade for cutting veneer plys, because they are more readily sharpened by local shops, do a nice job, and may be less expensive. TCG blades with a moderate number of teeth and positive hook are good for general purpose cutting and long life. There are also blades specifically for ripping solid stock that have very few teeth. And we also stock blades that are specifically designed for plastics- one that is designed for hard plastics like acrylics, with more TCG teeth, and one for soft plastics like nylon and polypropylene, with much fewer ATB teeth.
Routine maintenance is important for any machine, and even a Striebig requires some, albeit not very much. The first job is to remove the offcut pieces/scraps from within and around the saw. After that, the single most important piece of maintenance is to oil the machined guideways on which the saws travels. Just pour a little 20W motor oil on a rag and once/week wipe the top rail of the frame and the three sets of guideways on the beam. Do not worry about oil attracting dust! The wipers/scrapers that are around each bearing wipe the surface clean, so the bearings roll smoothly. Oiling the ways protects the bare steel and allows those wipers to glide smoothly along the rails and not jump and jitter (and potentially roll under a bearing) along the way. While you have the oily rag in hand, it’s good to also wipe the round column that the saw head plunges in and out on, and the plate that the parallel guides act on. Next, there are two grease points for the slide ball bushings use to plunge the saw head on that the round column. The grease gun for these fittings is included in the tool kit. Wipe the fittings and pump one shot of grease into each fitting once/month. Beyond that, all the bearings are sealed and don’t require maintenance. There is no lubrication for the shifting grid; no lubrication for the counterweight cables or the center shelf bar. Every so often you should make a visual check of the wipers and make sure they are all in place and in good condition. On models with an air supply, you will need to check the water reservoir and drain any water that may be collected there. If you do these few basic things your Striebig will run well for more than 30 years, as many still are!
Success Stories
Stiebig helps high-volume lumber & hardware store provide superior customer service
TH&H Hardwoods and Hardware